ARC FLASH RISK ASSESSMENT & LABELING
We provide cost-effective, comprehensive arc flash risk assessments for facilities of all sizes and industries throughout the United States.
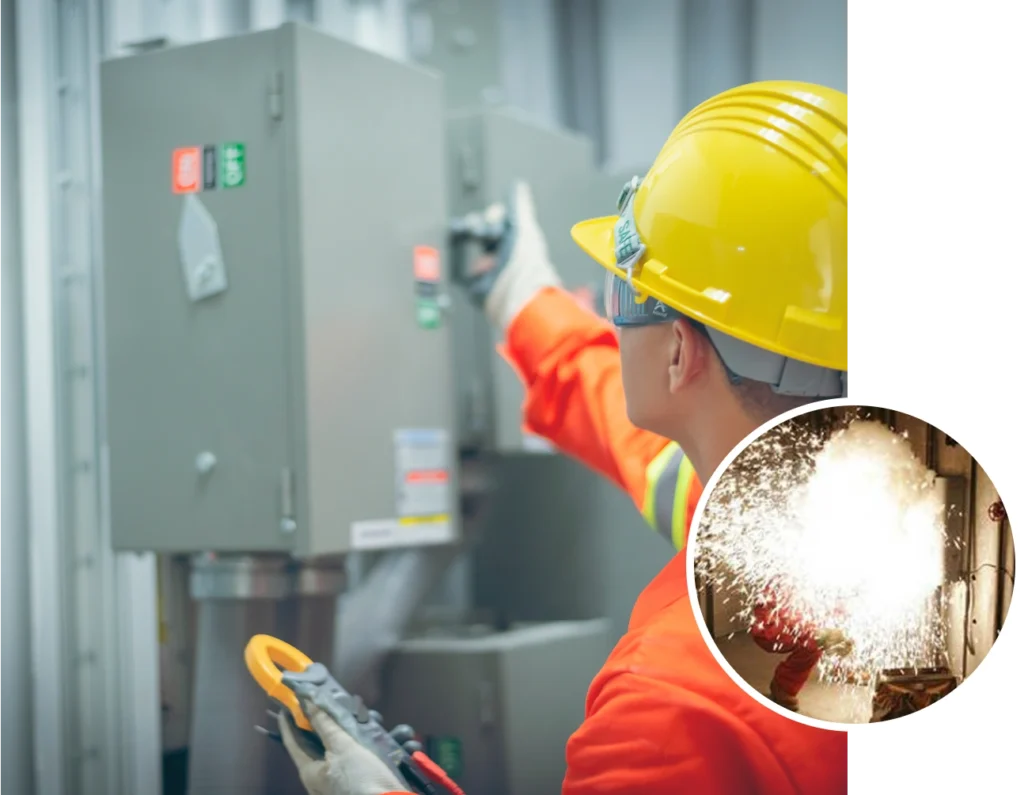
What is an Arc Flash Risk Assessment?
The facility arc flash risk assessment (AFRA) is formerly known as the “arc flash hazard analysis” or also referred to as an “arc flash study”.
The goal of this assessment is to identify arc flash hazards and create procedures to ensure the safety of all of your employees. NFPA 70E requires an Arc Flash Risk Assessment to be performed to identify and document potential arc flash hazards for all facilities with three-phase electrical power systems.
This standard covers every type of commercial, industrial, and institutional facility enterprise. This is currently required every 5 years, as well as when significant changes to the layout or equipment have occurred.
Jacman Group Safety uses a proprietary software to do the job faster, more precisely, and with less travel time. This efficiency allows us to be extremely competitive with pricing.
An Overview of Our AFRA Process
Jacman Group’s trained field experts come on-site and collect all necessary data from your electrical system.
A digital model is created of your facility’s electrical distribution system. This model is then used to complete the engineering analysis.
Multiple safety engineering analyses are performed including Short Circuit Analysis, Protective Device Coordination Analysis, Protective Device Interrupt Rating Analysis, and Incident Energy Analysis.
Customized, site-specific, NFPA 70E-compliant arc flash safety labels are created and applied to the electrical equipment.
The results are provided in both a printed and digital report, including any findings describing dangerous conditions within the facility and recommendations for mitigating these hazards.
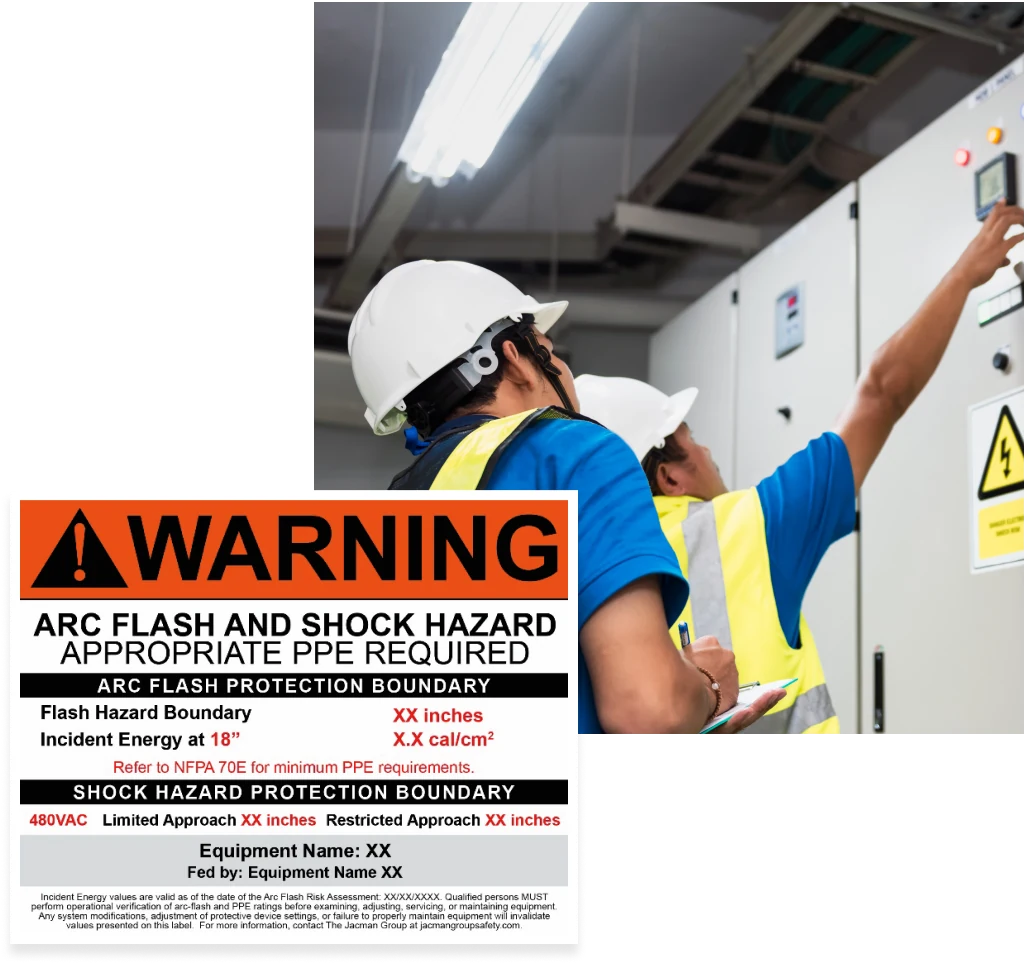
Get an Arc Flash Risk Assessment
Quote for Your Facility Today
How We Help You Ensure OSHA & NFPA Compliance
Many companies are coming to grips with a new electrical safety concern – arc flash safety. Often, the initial question that is raised by management is, “Does this even apply to our facility?”
In short, the answer is a resounding “yes”.
In the United States, OSHA can and does cite companies that do not provide protection for their employees against arc flash and arc blast hazards. Although the OSHA 1910 standard does not specifically define all of the procedures and personal protective equipment (PPE) necessary for a sufficient arc flash safety program, it does recognize the NFPA 70E standard as the best practices for implementation of a comprehensive electrical safety program.
We provide assistance to companies of all sizes to establish the required elements of an Electrical Safety Program including:
- Facility Arc Flash Risk Assessment
- Equipment Labeling
- Proper Arc Flash PPE
- Arc Flash / NFPA 70E Electrical Safety training
- Electrical Safety Facility Audit/Inspection
- Infrared (IR) Scan
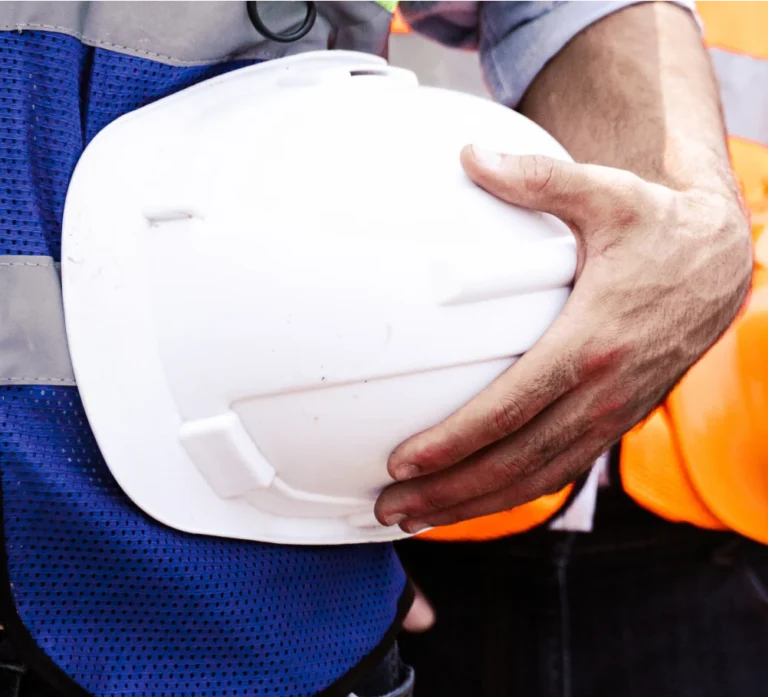
Arc Flash Risk Assessment Process
The goal of an Arc Flash Risk Assessment is to determine the level of hazard that exists at each electrical enclosure, such as a control panel, panel board, disconnect switch, or switchgear. There are several steps required to complete the assessment.
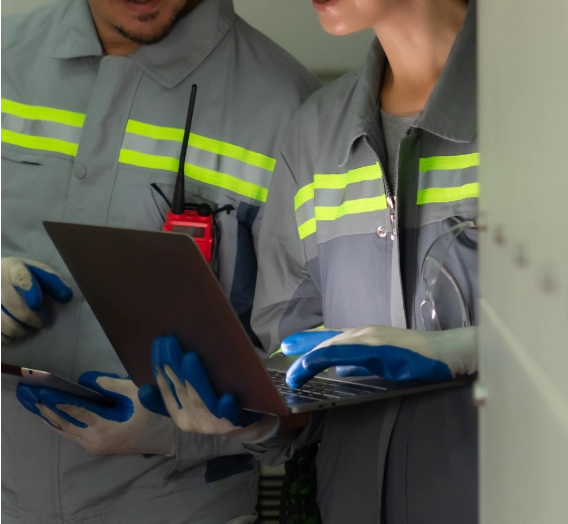
- Step 1
Data Collection
There is a variety of information required to correctly document the power distribution system.
This information includes data on circuit breakers, fuses, cabling, and end loads. Most companies do not want to de-energize in order to collect this data, as this task requires an experienced, skilled, and qualified individual or team.
Jacman Group Safety is committed to performing the data collection phase without causing massive interruptions, with years of expertise to back up our process.
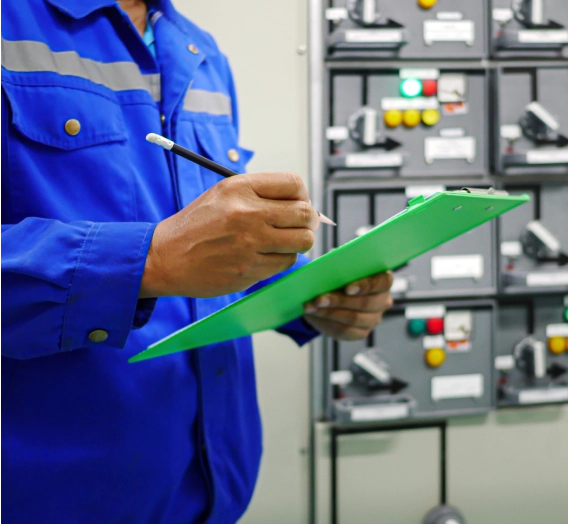
- Step 2
Arc Flash Risk Assessment
Most engineers conduct Arc Flash Risk Assessments by utilizing specialized software. In this phase, the engineer models the power distribution system based on the data collected. From this model, PPE categories, incident energy levels, and the arc flash boundaries for the electrical distribution system are determined.
Based on the study results, we analyze points in the system where the PPE Category 3 or above and make recommendations for possible system changes that would reduce the PPE category to an acceptable level. This is standard procedure for Jacman Group, as is a review of the system for any major system coordination issues and insufficient fault bracing of electrical system components. We will identify problems and report them as a part of the arc flash report.
The system model will allow for the addition of future information and study of the expanded power distribution system if desired. We recommend that the electrical engineer conducting this study have a background in power distribution and also be involved with other aspects of arc flash safety such as data collection and safety consulting.
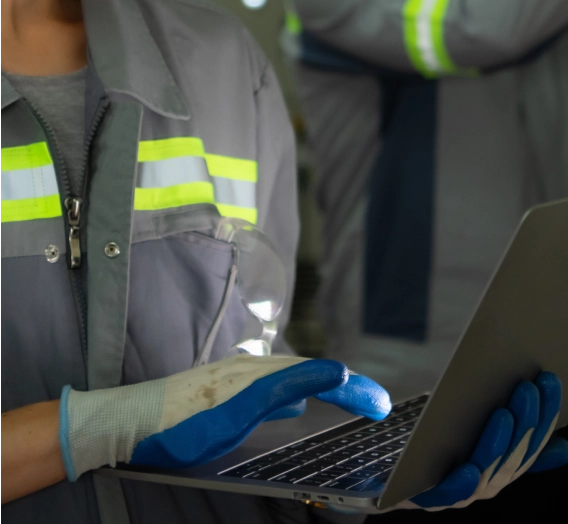
- Step 3
One-Line Diagrams
Our team utilizes industry-standard SKM Systems Analysis software to create detailed one-line diagram(s) of the electrical system. These are included with the project deliverables.
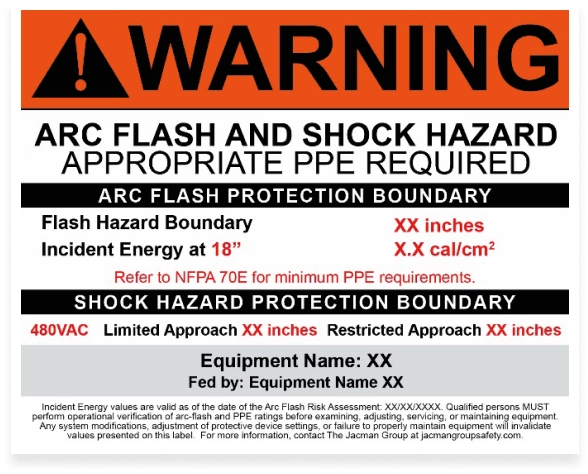
- Step 4
Equipment Labeling
Arc flash warning labels adhere to ANSI standards, and shall be affixed to all equipment included in the assessment.
Labels display the flash protection boundary, incident energy, work distance, required PPE level, and the shock hazard voltage and boundaries.
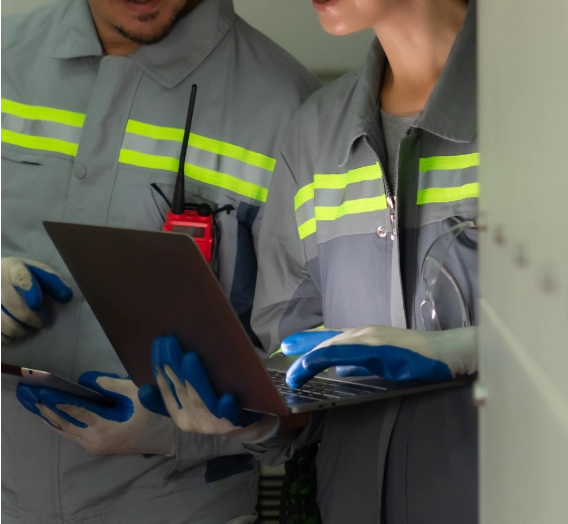
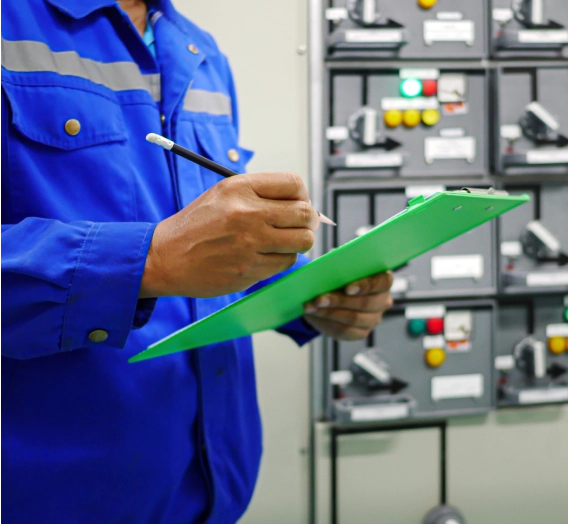
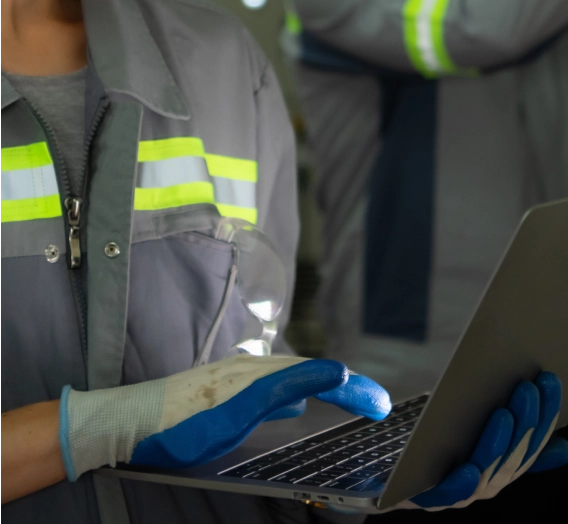
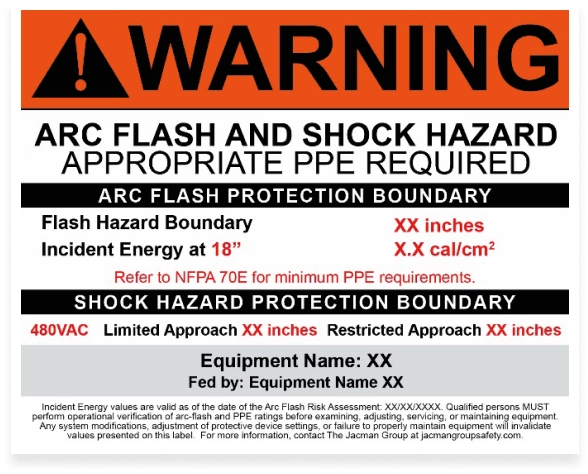
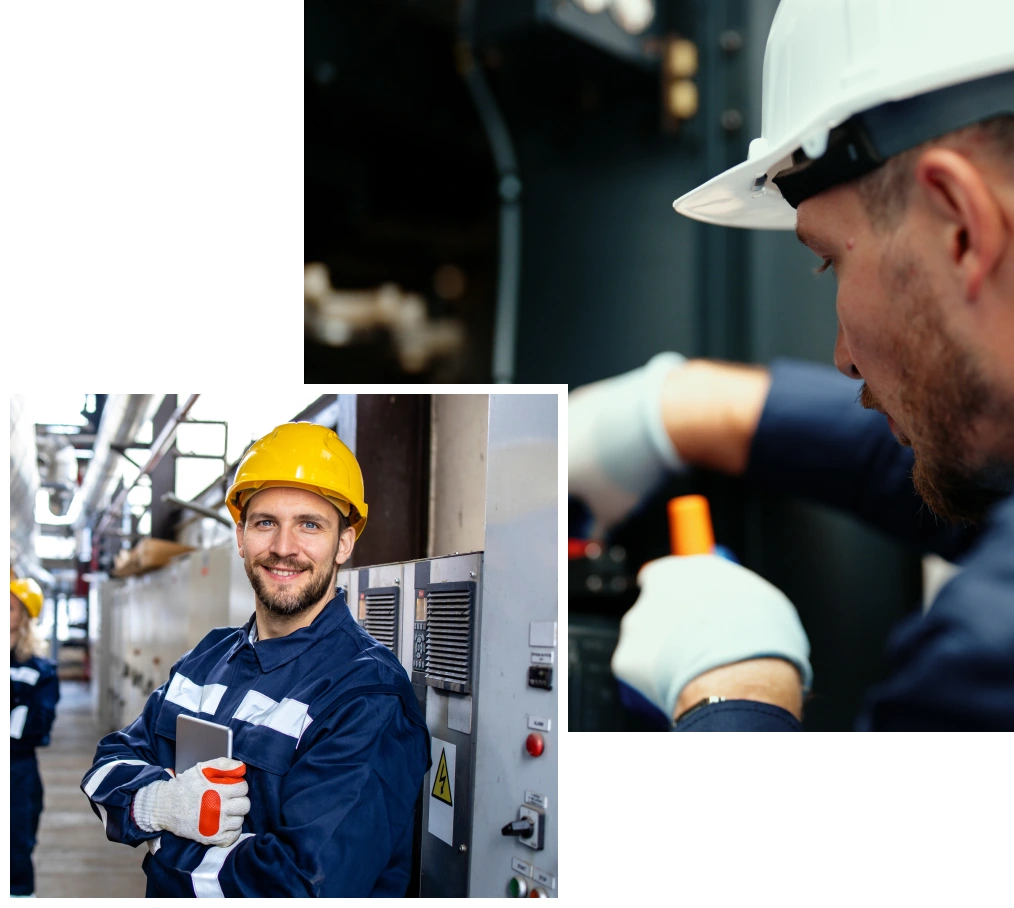
Post Arc Flash Assessment Support & Consulting
Regardless of how much time is spent in the data collection, analysis, consulting, and training stages, there are always other questions that arise.
Jacman Group Safety is here for you long after the completion of the project to answer any questions and continue to assist you through this ongoing process.
Our goal is to maintain the safety of your employees and facilities, and ensure continued compliance with OSHA and NFPA standards.
Infrared Electrical Scans & Surveys
An infrared (IR) electrical scan is an inspection that will identify hot spots in your electrical system. An IR study can be completed at the same time as your Arc Flash Study, if requested.
IR electrical inspections detect system overloads, loose defective components and damaged switchgear. Infrared thermography is used to find areas of excess heat (caused by increased resistance) so that problems can be corrected before a component fails, causing damage to the component, creating safety hazards and productivity loss.
Over time and as conditions change, this should be revisited to find and prevent issues before they cause damage to your personnel, equipment and facility as a whole. As always, proper maintenance is a critical component.
The IR survey should be conducted at least once a year, however, it’s highly recommended to perform at intervals of 6 to 8 months in an effort to capture operating characteristics within the constant temperature changes and atmospheric effects to the equipment.

Our Promise To You
Our goal is to help companies of all sizes achieve and maintain a safe electrical work environment. Feel free to reach out with any questions whatsoever. We’re here to help you!
- (877) 252-2626
- info@jacmangroupsafety.com